5 Benefits of Building with Cross-Laminated Timber
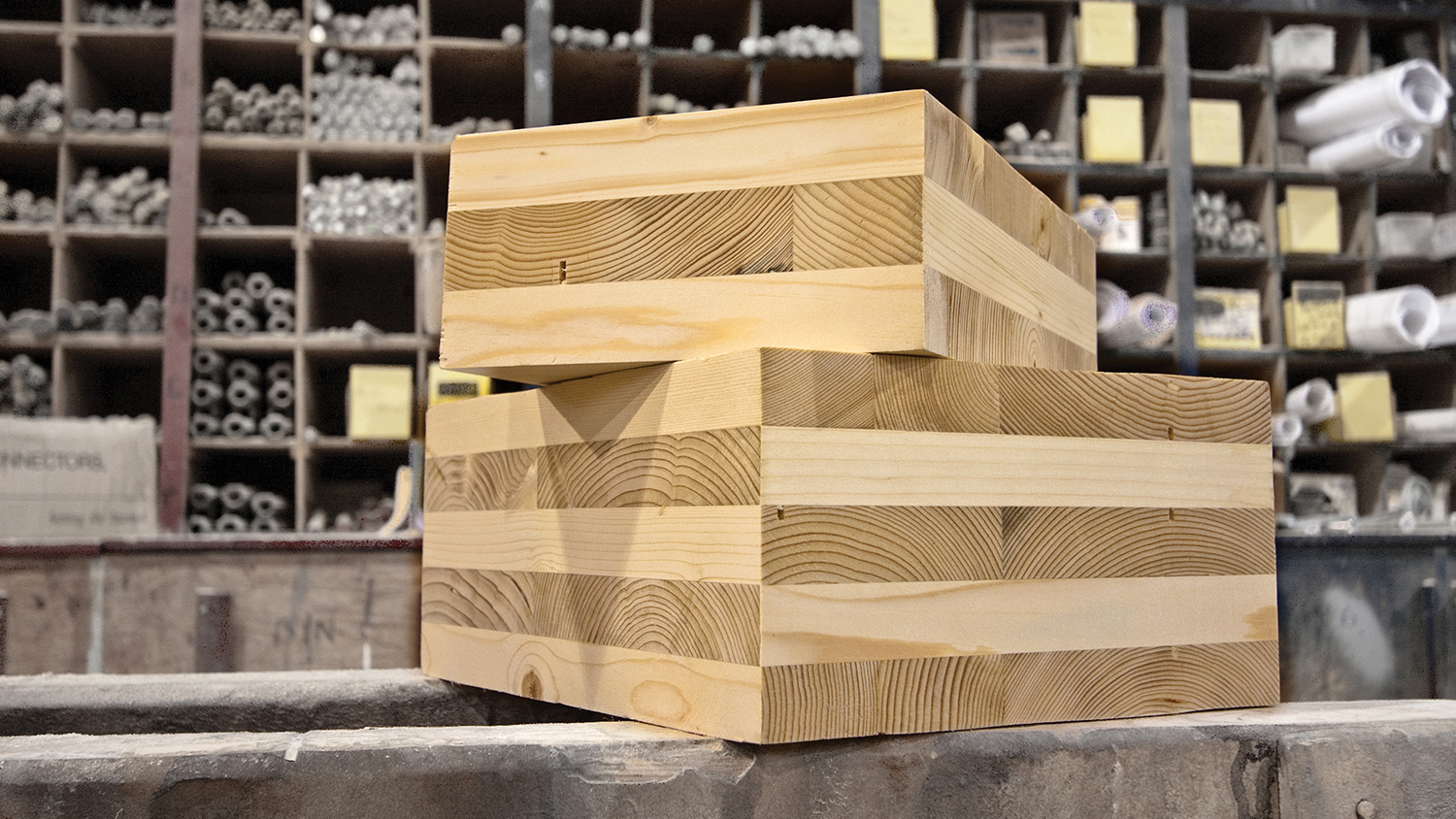
With construction accounting for nearly 40% of global carbon emissions — one of the primary drivers of human-induced climate change — designers, builders and other industry stakeholders are working to reduce their environmental footprint by integrating renewable materials and sustainable design into their projects.
Cross-laminated timber (CLT) is emerging as a popular material of choice for both residential and commercial structures across the United States. Originally developed in Europe in the 1990s, CLT is a wood product made of several layers of structural grade lumber that are arranged crosswise and glued together.
CLT is unique in that it has a strength-to-weight ratio that’s comparable to concrete, despite being five-times lighter. Since 2015, when CLT was first incorporated into the International Building Code, the material has been used as a sustainable alternative to form walls, roofs, floors and even ceilings.
Steve Kelley, the Reuben B. Robertson Professor in the Department of Forest Biomaterials at NC State’s College of Natural Resources, recently partnered with the U.S. Forest Products Laboratory to examine the financial and environmental benefits — and costs — of using CLT in tall wood buildings.
We spoke with Kelley, whose research focuses on the sustainable production of energy and materials from biomass, to learn more about the advantages of using CLT to construct houses and other structures — from fire resistance and seismic durability to carbon sequestration. Here’s what we found out:
Carbon Storage
Most scientists agree that greenhouse gas emissions from human activities, such as the burning of fossil fuels like coal and natural gas for energy, have accelerated global warming over the past century.
The manufacturing of building materials accounts for 11% of global greenhouse gas emissions, with the production of one ton of cement resulting in the emission of roughly one ton of carbon dioxide — the most abundant greenhouse gas in the atmosphere.
Because CLT is made of wood, it can store carbon during the building’s lifetime and even capture additional carbon. In fact, researchers have found that a hybrid, mid-rise CLT commercial building provided a 15-26% reduction in global warming potential, depending on the building design.
Kelley said wood isn’t as energy-intensive as steel and concrete, meaning the manufacturing process for CLT emits less carbon. Also, when the wood is harvested from sustainably-managed forests, CLT creates a circular carbon cycle.
Forests act as carbon sinks — trees remove carbon dioxide from the atmosphere and transform it into wood through photosynthesis. When trees are cut down and used to construct buildings, they continue storing carbon in the structure.
If a landowner plants one or two new trees for every tree cut down, the new growth starts another cycle of carbon sequestration that will last until the trees are harvested and incorporated into a structure as CLT panels.
Fire Resistance
With hundreds of thousands of structure fires occurring across the U.S. every year, the decision to use combustible wood for a construction project may seem risky. But research shows that properly designed CLT structures provide significant fire resistance.
A 2019 study published in the journal Wood and Fiber Science found that a CLT structure could withstand more than 90 minutes of burning before it collapsed. By comparison, a single-story wood-frame home collapsed after just 17 minutes.
Kelley said CLT acts like a large log on a campfire, with the thick panels burning slowly enough so that buildings remain structurally stable for extended durations when exposed to fire.
As the surface of a CLT panel is exposed to fire, it becomes a black layer of “char.” This layer acts as insulation, protecting the unburnt core of the panel from experiencing an excessive rise in temperature.
“The thicker you make CLT panels, the better they are at forming that protective char layer,” Kelley said.
Kelley added that additional fire protection can be added by encapsulating CLT with a protective layer of drywall, as is required to meet the building code requirements for taller wood structures.
Seismic Durability
According to the U.S. Geological Survey, about 143 million Americans live and work in areas where earthquakes could cause structural damage over the next 50 years — the average lifespan of a building.
Seismic performance of a building is related to the strength and weight of the building materials. CLT is a strong, tough, light-weight material with good performance in an earthquake, according to Kelley.
Additionally, because of its lightweight frame, a CLT structure isn’t likely to collapse as heavily on inhabitants during an earthquake compared to those made entirely of steel or concrete.
In 2007, a joint Italian-Japanese research team tested a seven-story CLT building on a “shake table.” They found that it could withstand the seismic forces of the 1995 earthquake in Kobe, Japan, which destroyed more than 50,000 buildings.
While CLT can provide an enhanced seismic performance, architects will frequently use a combination of materials to meet safety requirements.
In some applications, such as a floor in a tall building, the flexibility of wood is a limitation that can be overcome with the addition of one or two inches of concrete that will “stiffen” the structure, according to Kelley.
Faster Installation
The old adage “time is money” is especially true for construction projects, where a builder’s ability to make a profit depends on their ability to complete projects on a deadline.
Unlike concrete and other conventional construction materials, CLT panels can be prefabricated at an offsite manufacturing facility and then installed in a shorter time because fewer joints are needed between interior support elements.
Kelley said the installation process for concrete requires formwork, shoring and reinforcement with steel rebar. With CLT, on the other hand, a construction crew can crane the prefabricated panels into place, set connectors and then tie the components together.
In 2016, the University of British Columbia completed Brock Commons — an 18-story student housing complex incorporating a hybrid design of CLT with concrete and steel components — in less than 70 days.
“Because you can assemble the CLT layer by layer, you can put it into place pretty easily,” Kelley said. “That’s a huge advantage if you’re building in an urban area where you may have to shut down the surrounding street for a year or more.”
Kelley added, “By reducing the time of construction, you’re not only saving money but also keeping the community happy.”
Job Creation
America’s buildings are constructed from thousands of materials, many of them imported from China and other countries. While this outsourcing of materials can save money for builders, it negatively impacts U.S. employment figures.
Many U.S. companies outsource their manufacturing capabilities to other countries, causing American communities to lose potential job opportunities — a key factor for maintaining healthy economic growth.
Data from the Bureau of Labor Statistics shows that American manufacturing has already lost 7.5 million jobs since 1969. By using CLT, the construction industry can support jobs at local manufacturing facilities.
Kelley said CLT panels can be made from a variety of tree species found in privately-owned forests in both the Southeast and Pacific Northwest, some of which are managed for timber production.
Once the trees are harvested, they’re transported to local sawmills and manufacturing facilities for processing. At the same time the harvested forests are replanted to close the sustainability cycle.
“Both steel and concrete may be imported or shipped over long distances,” Kelley said. “As we develop this industry, the lumber should be coming from a manufacturing facility that’s just 50-100 miles away from the construction site.”
- Categories: