Daniel Saloni
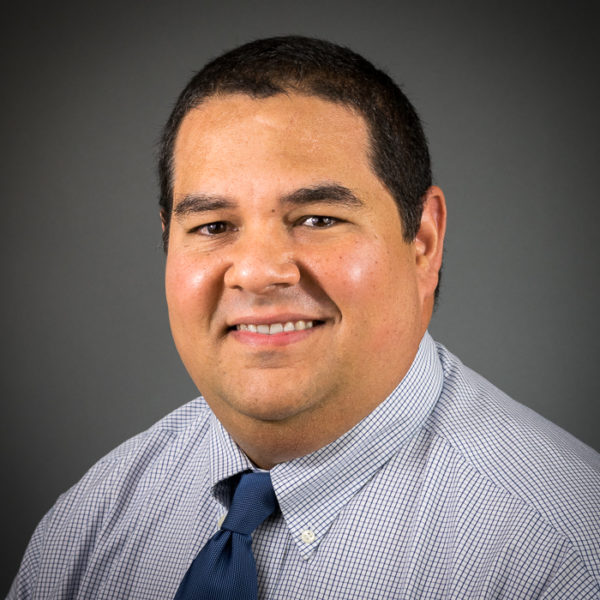
Bio
Dr. Daniel Saloni is an associate professor in the Department of Forest Biomaterials at North Carolina State University. Before applying to a faculty position at NCSU, he was a laboratory manager and research assistant in the Wood Machining and Tooling Research Program at North Carolina State University. Prior to joining NCSU, he was an assistant professor in the Department of Industrial Engineering and Junior Consultant in UCAB Consulting for five years at Andres Bello Catholic University in Caracas, Venezuela.
Dr. Saloni received his Ph.D. in Wood Science from the Department of Forest Biomaterials and a Master’s degree in Integrated Manufacturing System Engineering at North Carolina State University. He also obtained a bachelor’s degree in Industrial Engineering and a Master’s degree in Project Management at Andres Bello Catholic University.
He has published various papers and participated in several conferences on process improvement, supply chain, biomass and bioenergy conversion and additive manufacturing, which are his major research areas.
Dr. Saloni is currently a affiliated faculty at the Center for Additive Manufacturing and Logistics (CAMAL).
Area(s) of Expertise
Process improvement, supply chain, biomass and bioenergy conversion
Publications
- Comparing the impacts of wood and APMP non-wood fibers on the properties of hygiene tissue paper , CELLULOSE (2025)
- A Multi-Criteria Approach for Quantifying the Impact of Global Megatrends on the Pulp and Paper Industry: Insights into Digitalization, Social Behavior Change, and Sustainability , LOGISTICS-BASEL (2024)
- An economic analysis of bamboo plantations and feedstock delivered cost in the Southern US for the manufacturing of fiber‐based bioproducts , Biofuels, Bioproducts and Biorefining (2024)
- Characterizing value-added pellets obtained from blends of miscanthus, corn stover, and switchgrass , RENEWABLE ENERGY (2024)
- Co-pyrolysis of biomass and polyethylene terephthalate (PET) as an alternative for energy production from waste valorization , FUEL (2024)
- Enhancing tool life through innovative process control in wood-based machining , WOOD MATERIAL SCIENCE & ENGINEERING (2024)
- Environmental Sustainability Analysis of Rotary-Screen Printing and Digital Textile Printing , AATCC JOURNAL OF RESEARCH (2024)
- Evaluating chemi-mechanical pulping processes of agricultural residues: High-yield pulps from wheat straw for fiber-based bioproducts , INDUSTRIAL CROPS AND PRODUCTS (2024)
- From waste to advanced resource: Techno-economic and life cycle assessment behind the integration of polyester recycling and glucose production to valorize fast fashion garments , CHEMICAL ENGINEERING JOURNAL (2024)
- Life focycle assessment of Brazilian bleached eucalyptus kraft pulp: Integrating bleaching processes and biogenic carbon impacts , CLEANER ENVIRONMENTAL SYSTEMS (2024)
Grants
The hygiene tissue industry (bath tissue and kitchen towel) is an annual 39 million tons - USD 100 billion - global market with a forecast to grow ~ 3% per year for the next decade [38], [39]. Most hygiene tissue paper grades require the use of both long and short virgin fibers, which provide strength and softness respectively [8]. As an effect of global megatrends, the demand for non-woody biomass for tissue manufacturing will continue to increase [40], and agricultural biomass, which is perceived to be a sustainable option, can be an important source of short fibers for the tissue industry [41]. Therefore, the need to research and create knowledge on the handling and conversion of biomass sorghum and switchgrass to produce sustainable and high-end fiber furnish for the hygiene tissue industry. The proposed feedstock can be established to supply fiber at industrial scale.
The hygiene tissue industry (bath tissue and kitchen towel) is an annual 39 million tons - USD 100 billion - global market with a forecast to grow ~ 3% per year for the next decade [38], [39]. Most hygiene tissue paper grades require the use of both long and short virgin fibers, which provide strength and softness respectively [8]. As an effect of global megatrends, the demand for non-woody biomass for tissue manufacturing will continue to increase [40], and agricultural biomass, which is perceived to be a sustainable option, can be an important source of short fibers for the tissue industry [41]. Therefore, the need to research and create knowledge on the handling and conversion of biomass sorghum and switchgrass to produce sustainable and high-end fiber furnish for the hygiene tissue industry. The proposed feedstock can be established to supply fiber at industrial scale.
- Need for a uniform format for herbaceous feedstock - Briquettes and pellets are a great alternative as they provide compacted storage with a longer shelf live paving the way for lower transportation cost and year-round feedstock availability - NC already has X commercial pelletizing facilities that could be leveraged as feeding pipelines to a larger national industry of value-added herbaceous biomass
In North Carolina, poultry is the top agricultural industry with an economic impact of more than $37 billion, employing over 146,000 people. Although, the main heating fuel for poultry houses is propane, recent pilot studies in the state have shown that wood pellets may be a cheaper heating fuel. Anecdotal evidence also suggests that wood pellet-heated poultry houses also produce better chicken survival, health, and growth. Our goal is to comprehensively assess the technical and economic feasibility of producing pellets specifically for the poultry industry in the Western NC, where a great proportion of broiler and ���������������backyard������������������ poultry farms are located. As the economics of poultry farming is heavily dependent on mortality and overall growth/productivity of chicken, we will examine how wood pellet-based heating affects indoor air quality and health of the broiler chickens in the poultry houses. Our project results will demonstrate if this fuel is cost-effective and sustainable for poultry production to facilitate decision-making about poultry house fuel selection. Additionally, our project will generate information about potential income enhancements associated with pellet-based poultry heating.
World energy demand has been continuously increasing, with no indication of slowing down in the coming years. There exists an imperative need for cleaner, sustainable, renewable energy sources that can be locally produced. Biomass is identified as a sustainable long-term plan to reduce the dependency on imported energy and as a national security strategy, and wood pellet is identified as an important biomass product with growing demand and an established expert market mainly in Europe. Many bioenergy-focused field studies conducted by NC State University have shown the efficacy of Populus as short rotation woody crops (SRWC) when clones are matched to site conditions. The objectives of this project are to develop a novel preprocessing during pellet production, assess its effects on the technical feasibility of wood pellet production, and evaluate potential of utilizing Populus clones that are suitable and highly productive in NC for producing the next generation of solid fuels. The expected outcomes include validity of the modified production method to improve the quality of wood pellets and identification of poplar clones for producing high-quality and durable pellets.
The main objective of this work is to perform a comprehensive characterization of wood materials based on standardized tests such as mechanical tests, compression under hot-press at various conditions, surface characterization and product inspection. In addition, we will perform a material preparation and conditioning prior to processing to assure consistency throughout the performance of the work. We will utilize equipment and machines listed in the facilities and other resources document.
This project will develop new sensor technology to directly assess feedstock quality characteristics, including chemical composition that will be coupled with process data in an advanced statistical process control framework, enabling production of consistently high-quality feedstock at reduced cost. With information on feedstock properties available at various points along the supply chain, more accurate cost analysis will be conducted along with life-cycle analysis of the feedstock production systems.
The manufacturing of MDF and HDF with UF resins and PMDI resins results in different machinability of the fiberboards. One method of assessing machinability is edge panel quality after processing with a router. This is illustrated in the photos included. Both adhesives result in boards that meet physical property standards such as IB, TS, MOR and MOE but, it is observed that these boards machine differently. The use of hardwood versus softwood species also influences machinability. Perhaps the resin loading level and distribution of resin on the fiber surface influences machinability. It is important for both resin suppliers and MDF/HDF manufacturers to understand the way these resins interact and adhere to fibers and the how they affect properties like machinability.
The CNR torrefaction machinery at Lake Wheeler Field Laboratory will process up to 6000 lbs. of Miscanthus pellets/Arundo donax grass and unspecified biomass pellets supplied by Jacobs Engineering. These results will be provided to Jacobs as part of an EPA project administered by Jacobs Engineering.
Additive manufacturing is a relatively new manufacturing process by which components are fabricated directly from computer models by selectively depositing and consolidating or curing raw materials in successive layers. Currently, the polymer based additive manufacturing industry mainly uses petroleum based filaments. Traditionally materials such as acrylonitrile butadiene styrene (ABS), polycarbonate, and Nylon are created from petroleum, a limited and nonrenewable resource, and dominate the marketplace for traditional manufacturing methods such as injection molding. Recently, biopolymers that are more sustainable, such as polylactic acid (PLA), have started to gain traction as a competitor to these traditional synthetic polymers. The main goal of this project is to design, evaluate and characterize the use of biopolymers enhanced with cellulose nanofibril (CNF) for additive manufacturing in order to provide more sustainable products. CNF will act as a reinforcing component to increase MOR/MOE, and also change crystallization rates and crystal size. The main outcome of this project will be a clear understanding of the sustainability aspects of enhanced biopolymers with CNF intended for additive manufacturing