Richard Phillips
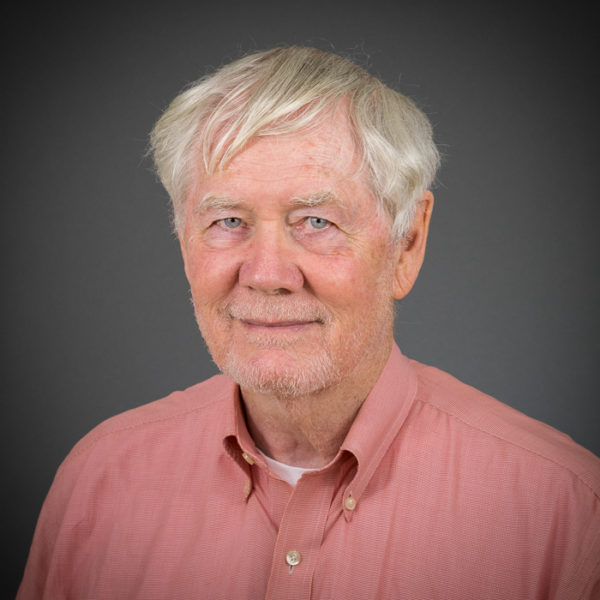
Bio
Dr. Richard Phillips is Adjunct Professor and Executive in Residence in the Department of Forest Biomaterials at North Carolina State University, having retired as Senior Vice President-Technology and Manufacturing from International Paper.
Additionally, Dr. Phillips was a board member of Illim – IP Russia JV. Currently, Dr. Phillips teaches Strategic Business Practices in the Pulp and Paper Industry at NCSU and provides leadership and critical thinking across the Department. Dr. Phillips is an on-demand consultant for the forest product industry.
Area(s) of Expertise
Cost and financial analysis of pulp/paper and biorefinery operations
Grants
The use of bio-bulk is proposed as a bio-based additive to considerably upgrade furnish properties for the manufacturing of hygiene tissue. Preliminary lab analyses show that by adding 4% of bio-bulk to tissue furnish, softness and bulk can increase by 15% and 12% respectively. As softness and bulk are important drivers for price on the shelf for hygiene tissue products, herein we propose a research project to evaluate the use of bio-bulk to upgrade tissue furnish, estimate the impact on final product price and develop the data set needed to file invention disclosure and patents. Our preliminary and conservative estimation values bio-bulk at ca. $4,000 per ton.
The demand for corrugated packaging materials has declined by only 8% from the peak, but production has actually increased slightly due to increased export markets. It is expected that in the future there will be increased demand for linerboard. Any concept that can increase the end use properties or the overall yield will have a significant impact on linerboard production cost and use. It is being proposed that the yield can be increased from 55 to 60% by raising the kappa # from 100 to ~ 140. However, this increase causes poor bonding and low board strength due to the lack of available bonding sites. Thus, it is being proposed in this project to substantially modify the surface lignin so that the fiber bonding can be improved without a concomitant significant loss in yield. The yield increase would be very significant, but these modifications do not require a new process to replace the existing kraft pulping process. In this proposal, we are suggesting the use of selective lignin reactions that can be easily retrofitted into a kraft pulping process to achieve high bonding while maintaining high yields. The methods that are being recommended include: ��������������� Atmospheric and pressurized oxygen delignification ��������������� Oxygen delignification reinforced with transition metals ��������������� Hydrogen peroxide with Fenton������������������s chemistry ��������������� Ozone ��������������� Soybean peroxidase Finally, we intend to provide a detailed techno-economic analysis of the different options that include both cash flow and capital cost analysis for possible mill implementation.
Evaluate the economics of producing sugar building blocks from cotton residues and compare versus commercial alternatives.
While several biochemical conversion process to produce liquid biofuels from biomass have been developed, there remains a significant challenge to design financeable projects. One of the most significant opportunities in achieving this goal is better utilization of lignin-rich process residue generated during the conversion process. Because financially attractive cellulosic liquid biofuels production remains elusive, many researchers are appropriately shifting focus to fermentation products with product value greater than liquid biofuels. Some commercial applications have emerged, though it is not clear how competitive the economics of the bio-products are, compared to traditional manufacturing routes. Relatively little research attention has been given to improving the economics of biofuel production by upgrading the portion of biomass that cannot be converted to the primary product. With woody biomass feedstock, the residue may constitute up to 50% of the original feedstock. The residue consists mainly of lignin (up to 80% of the residue). Traditional techno-economic analyses logically consider burning the residue in a biomass boiler to generate process steam and power. While useful, and may be valuable to claim a ����������������Green��������������� product label, combustion is the least economic route for residue utilization. With low natural gas prices in the United States, residue may be better upgraded into other value-added products. From an existing problem in the emerging cellulosic biorefinery industry to an opportunity to enhance economic operations in the already established pulp and paper industry, this novel process can trigger important financial impact to biomass converting facilities. For example, the kraft pulping process is the dominant pulping process, accounting for 98 percent of chemical pulp production in the United States and 92 percent of chemical pulp production in the world [1]. In 2011, the world pulp production was over 180 million metric tons and the United States produced around 50 million metric tons [2]. About 50 million tons of lignin are produced annually by the pulp and paper industry. While about 1 million tons of lignosulfonates from sulfite pulping and less than 100,000 tons of kraft lignin are commercially exploited, the majority of technical lignin (mainly kraft) is burned at the same factories for chemical and energy-recovery. While chemical and energy recovery is essential for the economic viability of the kraft process, a portion of lignin can be separated from the process if high value can be found for its uses. Interest in kraft lignin as an alternative to replace phenol in phenol-formaldehyde (PF) resin has remained strong over the last decades because of the structural similarity between lignin and phenolic resin. In the other hand the use of high value lignin products can be used to improve the economy the emerging lignocellulosic based biorefinery industry.
The production of bio-based materials (including solid and liquid biofuels) in the U.S. has been identified as a national priority as means to reduce dependence on foreign oil. During 2011 the United States produced almost 14 billion gallons of bioethanol for transportation fuel (all of this produced from starch-based corn kernels). Despite the success in bioethanol production, there are several societal concerns regarding the sustainability of producing bio-based materials and fuels from corn kernels, as well as polemic around the use of food based materials for fuel production. The 2008 USDA report titled "U.S Bio-based Products Market Potential and Projections through 2025" clearly identifies lignocellulosic biomass as an important and potential source of building blocks for the production of hundreds of bio-based materials and fuels that could replace petroleum based materials. Furthermore, lignocellulosic feedstock has been identified as the main raw material for second generation biofuels (based on cellulosic biomass), with mandates to produce 16 billion gallons by 2022. Production of 0.5 and 1 billion gallons cellulosic biofuels are expected for 2012 and 2013, nevertheless as the third quarter of 2012 there is no a single commercial facility in the US. Several barriers have been identified for the commercialization of cellulosic biofuels as: high capital expenditure (CAPEX) or capital investment, which translate into longer paybacks of 8-11 years with minimum ethanol revenue (at 12%) above current market prices. Other limiting factors include lack of proven technology at industrial scale which increases uncertainty in production yields, operation costs and CAPEX, as well as high enzyme cost and feedstock cost and availability. Lastly it is well known and discussed by experts in the area that the productions of commercials byproducts are required to offset operational costs and reduce the impact of CAPEX. There have been several attempts for commercialization of cellulosic biofuel biorefineries, and so far all have resulted in financial and technical fiasco with hundreds of millions dollar of public and private funding lost. Furthermore, the intensive funding provided by federal, state and private entities in the last ten years have resulted in the generation of arrays of technologies (and hybrids technologies) that promise to solve some of the current limitations to profitably produce transportation biofuels and other bio-based materials. The evaluation of potential technologies linked with potential business models are required to advance in the commercialization of liquid transportation biofuels and other bio-based materials, these tasks require of high trained talent in conversion process, technology management and business models, requiring intensive course work in engineering, science and business. The main goals of this proposal is to develop an educational program for a new generation of technical to commercialization researchers who understand the entire value chain of bio-based materials & fuels science and engineering, and the corresponding technology management and business models needed to meet the future national needs for technologically advanced scientists in the area of bio-based materials and fuels.
The main objective is to develop cost effective pretreatments for non-woody biomass that can be integrated into a repurposed or greenfield ethanol mill. The ability to handle multiple feedstocks will ensure the operation flexibility with the increased total amount of biomass for conversion thereby improving the overall economics. In addition we will improve overall carbohydrate conversion in enzymatic hydrolysis and also to increase the sugar concentration.
Biochemical routes to cellulosic bioethanol have not achieved commercial success, despite now many years of laboratory and pilot plant development. Our past studies on Repurposed Kraft Pulp Mills converted to ethanol production using kraft Green Liquor (GL) Pretreatment highlighted how capital requirements can be reduced by re-using existing kraft mill assets, while a Greenfield application of the same technology would not have a financeable internal rate of return due to high capital cost. This work also pointed promising directions for simplification of the process, reduce capital, and bring a Greenfield GL option into consideration. Our unique approach to Biomass-to-Bioethanol takes advantage of proven Pulp and Paper processes and equipment, coupled with our experience and understanding of what makes technical and financial sense. We propose a Consortium of targeted industrial partners join with the Principal Investigators to execute a new two-year study (an extension of our existing body of work) to capital-efficient ethanol conversion processes coupled with both woody biomass and agricultural crops with potentially excellent financial returns for Greenfield Biomass-to-Ethanol plants. Companies with future business opportunities in bioethanol production should have significant interest in supporting this work. WERC II first objective is to prove at the lab scale the technical and financial impact of our ideas to reduce capital and enzyme dose and increase ethanol output. Examples of improvement include: (1) reduced feedstock cost through multiple feedstocks (base load hardwood chips, supplemented by agricultural residues during harvest season); (2) process simplification by use of gravity clarifiers that use polymers to settle and thicken lignin - in place of the lignin filter we have considered in the past; (3) employment of simultaneous saccharification and fermentation in place of separate steps as incorporated in our current model. Funding WERC II will allow us to inform our existing simulation models with improvements that we can support from the lab work. A second objective is to reduce the overall feedstock cost by incorporating agricultural crops and/or their harvest residues. Our total process approach offers three alternatives introduction sites for the non-wood crops. Sweet Sorghum is viewed as one of the most promising because of the high sugar content of the cane as harvested, but also the relatively high carbohydrate content of the bagasse residual after crushing and squeezing the sugar. A third objective promises a more dramatic improvement possible by incorporating acetogenic fermentation in place of the more common ethanologenic fermentation. While acetogenic fermentation of sugars to acetic acid is well-studied, process technology to convert acetic acid to ethanol is largely proprietary to ZeaChem, and will undergo continuous Pilot Demonstration Unit demonstration Q1 2011 in Boardman, OR. While more capital and energy intensive than the more common ethanologenic route, we project superior financial performance because the acetogenic route is inherently 50% more efficient than ethanologenic. The higher output reduces the cost per unit product of all the major cost areas, including Capex per gallon. WERC II funds will allow refining our existing acetogenic model, and populate the model with actual laboratory fermentation results. Models predict ethanol yields greater than 100 gallons per BDT Mixed Southern Hardwoods feedstock, or roughly 50% higher than theoretically possible with conventional ethanologenic fermentation systems.
This project utilizes the papermaking and paper recycling process as an extremely advanced and fortuitous pretreatment to produce highly accessible and mainly lignin free carbohydrate material as a feedstock for ethanol production. This avoids landfill costs of the sludge and produces valuable products, resulting in a predicted 40% internal rate of return. We will first characterize a variety of industrial sludges originating in North Carolina and surrounding states for ethanol production potential. We will then in the lab and pilot plant evaluate/demonstrate the fractionation of the sludge into two valuable streams, a carbohydrate rich stream for ethanol production and a carbonate rich stream for crop land applications. Enzyme hydrolysis and fermentations at lab scale will determine the fractionated carbohydrate stream?s ethanol potential. We will then evaluate an industrial sludge of high potential at the truckload level for an extended continuous NCSU pilot plant evaluation. A rigorous economic evaluation will be developed and utilized to justify an industrial processing plant. Advanced Residual Management, expects to utilize successful findings of this project to justify the investments required to build and operate a commercial facility.
Pulp and paper industry in the United States is currently in significant decline in product demand and profitability due to several reasons, including electronic substitution and changes in generational consumption patterns. More than 15 million tons of capacity have been permanently closed since 2000 and each mill closure represents the loss of hundreds of direct jobs at the mill and thousands in the local area, but also leaves significant capital equipment in place for wood processing, pulp production, steam and energy production, and wastewater treatment, all of which can be re-deployed for ethanol production without significant compromise. Therefore, the risk in capital and biomass supply can be significantly reduced. We have investigated repurposing kraft pulp mills to produce ethanol from woody biomass in detail and have shown attractive internal rates of returns higher than 20% and cash cost about $1.60 per gallon of ethanol. To extend this effort, we propose to investigate the efficacy of a repurposed kraft mill that integrates non-woody biomass with woody biomass into the process for ethanol production. We will develop a process that is capable of handing both woody and non-woody biomass and the ability to handle both feedstocks will increase the amount of biomass available for conversion, improving the overall economics. Deliverables include process performance using woody and non-woody biomass in a repurposed kraft mill, a simulation model from biomass harvest through final product, capital cost estimation, and a financial investment model for potential investors.
This project is focused on: the production of fuel ethanol and acetic acid from woody biomass available in North Carolina and the subsequent combustion of the extracted wood chips. Evaluate the potential for producing ethanol by the extraction of hemicelluloses prior to combustion using an integrated process/capital /economic cost model for the extraction, fermentation and combustion of biomass. The best processes operating conditions and the equipment cost will have to be established to determine economic viability for using the above process at different locations in North Carolina that have the potential for biomass combustion