Campus Sustainability in Action: Recycling 3D Printing Waste
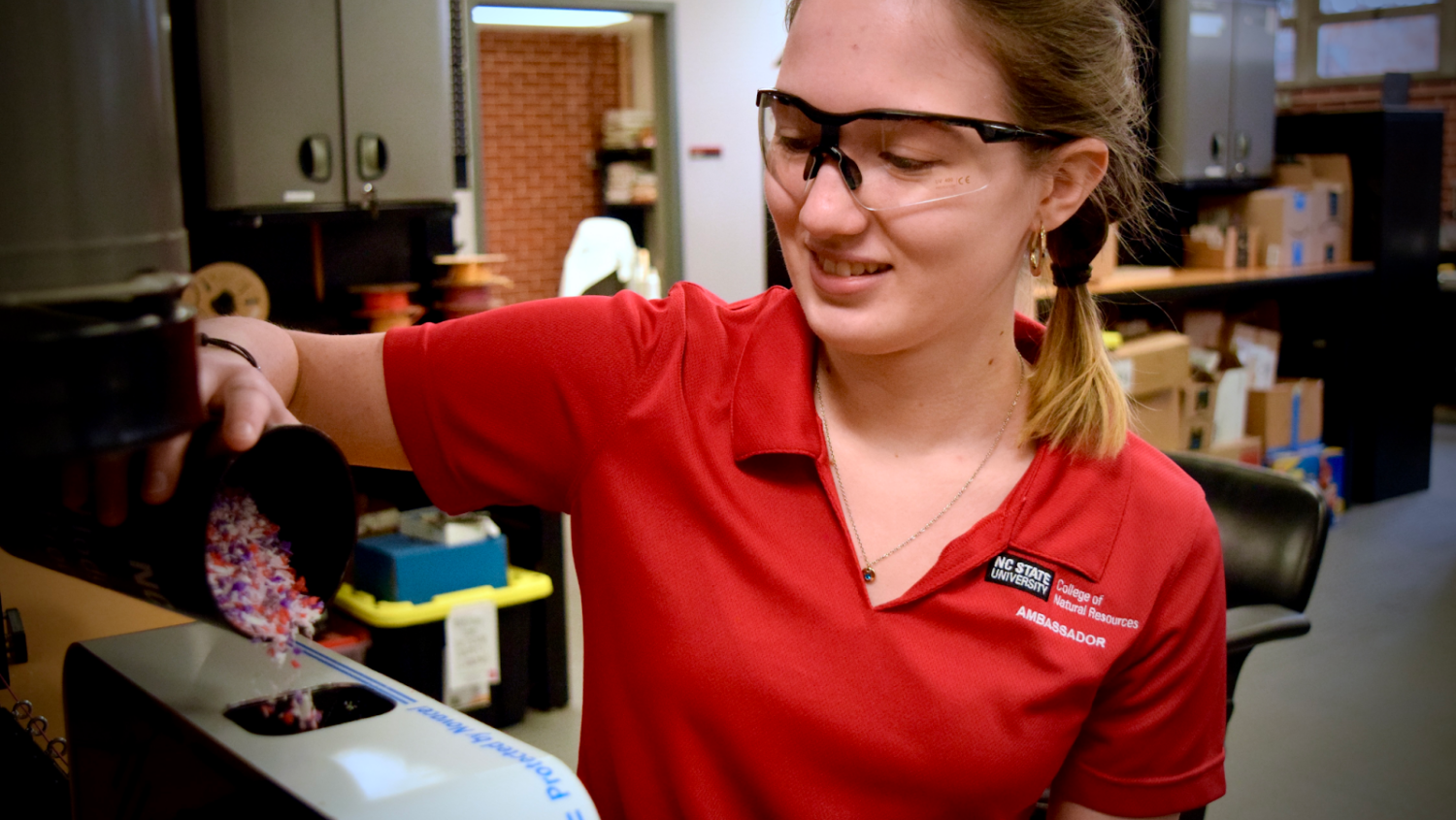
In the sustainable materials and technology (SMT) program, students develop hands-on skills to tackle environmental challenges, including waste reduction and material reuse. One critical focus is recycling thermoplastics, which are plastics that can be melted and remolded into new products—offering a sustainable alternative to traditional disposal methods.
At NC State’s Hodges Wood Products Lab, home to the SMT program, Dr. Daniel Saloni leads the Sustainable Manufacturing Lab, where undergraduate researchers explore innovative ways to recycle plastics. Dr. Saloni has previously collaborated with recent graduate, Bella McInnes, as well as current junior, Catherine Kirch, to tackle projects focused on enhancing plastics recycling on campus. Bella and Catherine competed in the Make-a-Thon competition in Spring 2024, where they came up with the idea of recycling both polypropylene coffee cups from on-campus cafes and PLA (polylactic acid) 3D printing scraps from the on-campus Maker Studio and Makerspace into recycled 3D printing filament. Both projects have been taken into development, where Catherine now works on expanding on their PLA 3D printing waste recycling pilot program in collaboration with the D.H. Hill Library Makerspace and Hodges Wood Products Lab.
From Waste to Innovation: Catherine’s PLA Recycling Process
Catherine partners with the D.H. Hill Library Makerspace, which offers 3D printing services for free for NC State students. The 3D printing process naturally produces waste material, mainly supports used in complex prints and failed 3D prints. These supports, though essential, are typically discarded, contributing to landfill waste. However, because PLA is a thermoplastic derived from corn, it can be industrially composted or remelted for reuse, making it an ideal candidate for sustainable recycling on campus.
The process, while rewarding, comes with challenges. Initially, Catherine had to haul large boxes of discarded supports across campus, a time-consuming and labor-intensive effort. Thankfully, the waste is now shipped directly to Hodge’s, where she sorts, processes, and refines the material.
The recycling workflow includes:
- Sorting the material – Scraps arrive somewhat pre-sorted by color, reducing contamination.
- Grinding the PLA – The material is shredded multiple times for a uniform particle size, ensuring consistent filament quality.
- Blending with virgin PLA – To enhance strength and usability, 10% virgin PLA pellets are added before extrusion.
- Extruding new filament – The mixed material is melted and spooled onto recycled filament reels for reuse.
This process not only reduces on-campus plastic waste but also demonstrates a real-world application of circular economy principles, where materials are continuously reused rather than discarded.
Scaling Up: Competing for Funding and Innovation
To expand her impact, Catherine has formed an interdisciplinary student team at NC State to compete in innovation competitions and apply for grants, including the NCSU Sustainability Fund Grant and the WEGE Prize competition. Through these efforts, the team is not only refining the recycling process but also securing funding for advanced machinery to scale operations.
Catherine’s initiative is also gaining traction within the university, as she collaborates with faculty and sustainability groups such as the Sustainable Materials and Technology Student Association (SMTSA) to improve campus-wide plastic recycling. In the meantime, she continues to produce recycled PLA keychains—both to promote the SMT program and to raise awareness about the potential of sustainable materials.
With growing support and innovative problem-solving, Catherine’s work showcases how SMT students are pushing the boundaries of sustainable manufacturing and paving the way for a greener future.
This article was written by Jack Zimmerman for the Department of Forest Biomaterials