Chancellor’s Innovation Fund Supports Six Promising Projects
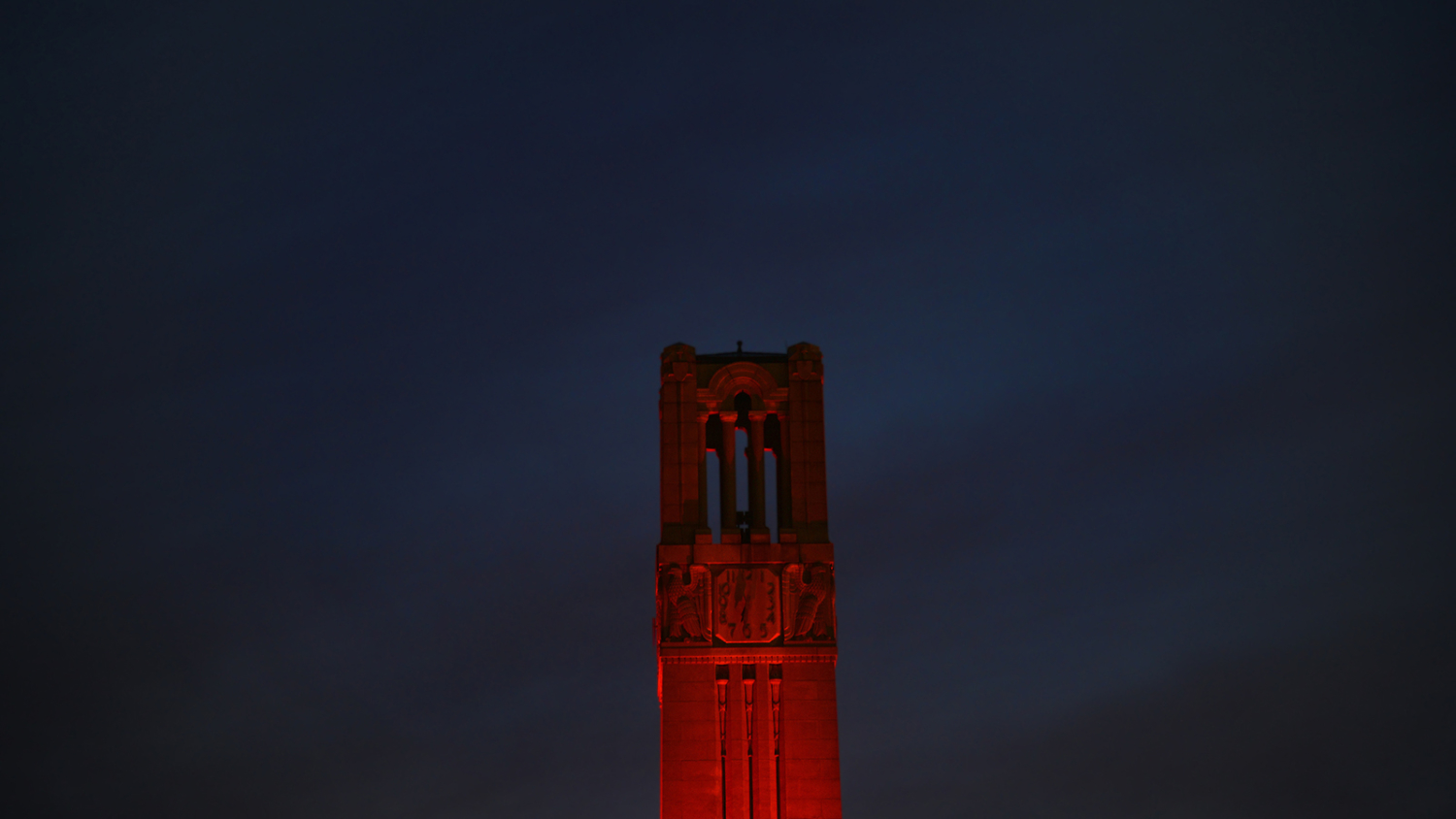
Research that starts at NC State doesn’t end here. The Chancellor’s Innovation Fund (CIF) is one way we work to ensure our research reaches the places it’s needed.
“As a land-grant university, our mission is to positively impact the lives of the residents of North Carolina and beyond by commercializing state-of-the-art research to solve societal problems,” says Wade Fulghum, assistant vice chancellor of the Office of Research Commercialization. “The Chancellor’s Innovation Fund — which has a very successful 10-year track record, generating $18 in additional research funding or investment for every dollar awarded — plays a critical role by providing funding to translate technologies to a point where a startup can be formed for commercialization or a license can be executed with an existing company.”
The CIF, launched in 2010, provides seed funding to a select few NC State research projects each year that have promising potential for market success. The goal is to help this research bridge the critical gap between public and private funding, ultimately creating products and technology that aim to tackle today’s most pressing problems.
To date, the CIF has granted nearly $3.4 million to 51 projects — which have attracted over $60 million in follow-on funding. These projects have generated 27 startup companies, 52 license agreements and more than $1.5 million in licensing revenue.
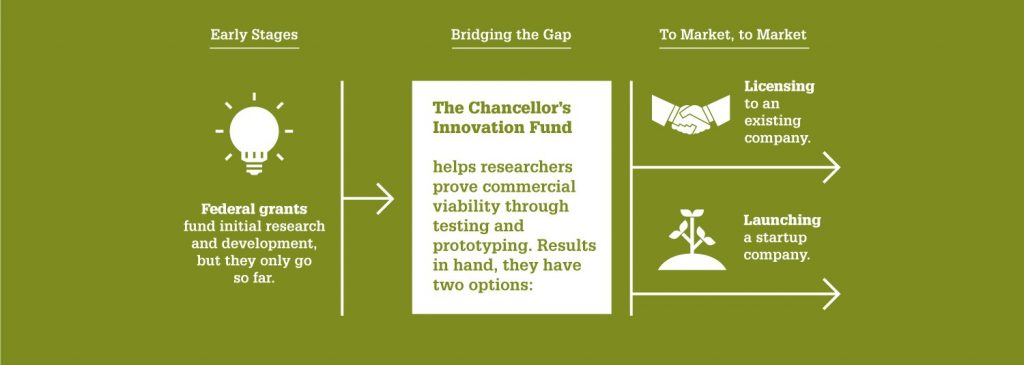
From safer treatments for human and animal health to novel manufacturing methods for toilet paper, lightweight car frames and synthetic fuel, read about the discoveries of this year’s CIF winners below.
RNA-based Anticoagulants
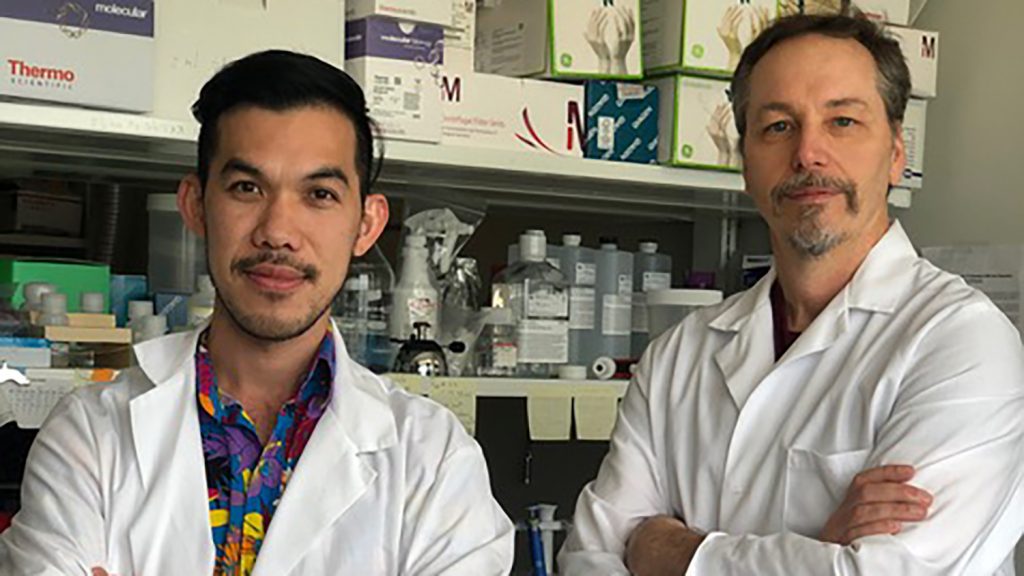
Most surgeries require carefully controlling bleeding and clotting — simultaneously reducing risks of blood clots and blood loss. However, the conventional anticoagulants surgeons commonly use provide a narrow treatment window, are associated with unpredictable side effects and typically lack a safe, specific antidote.
Thom LaBean and postdoc Abhichart Krissanaprasit, of the Department of Materials Science and Engineering, have created functional RNA origami structures that act as effective anticoagulants. The RNA-based anticoagulants are more predictable and much easier to reverse — with safe, specific antidotes. The technology has the potential to reduce the risk of complications and decrease patients’ length of recovery time.
LaBean and Krissanaprasit have founded a startup company called Helixomer to pursue commercial development of the new drug. CIF support will be used to perform FDA-required animal trials, testing efficacy and pharmacokinetics prior to human trials.
A New Form of CRISPR
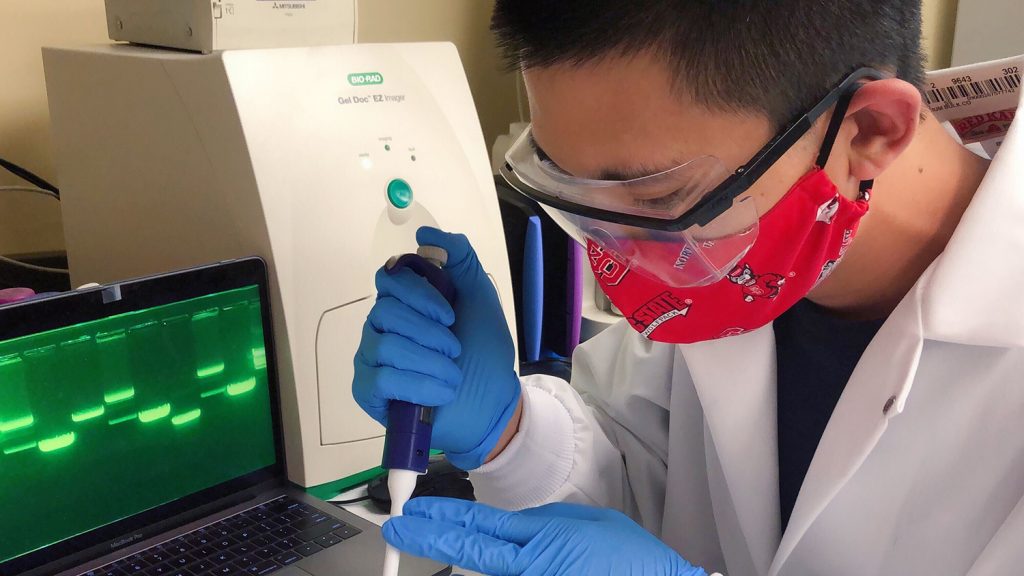
Most CRISPR-based gene-editing platforms fall into one of two categories: Type I, which work like a saw; or Type II, which work more like scissors and therefore are more precise but not as fast. Relatively little research has been done on Type III CRISPR platforms.
Gavin Williams, of the Department of Chemistry, along with Chase Biesel, of the Department of Chemical and Biomolecular Engineering, and graduate assistant Zhongtian Zhang have created Sery-CRISPR — a novel Type III platform that has unique applications, including rapidly editing microbial genomes to produce drugs and other therapies.
Williams likens Sery-CRISPR to a “Swiss Army knife” because it could have cutting abilities similar to those of both Type I and Type II CRISPR platforms, and says it could be faster and easier to use compared to current technology. And as a Type III platform, Sery-CRISPR is not subject to the intellectual-property disputes surrounding Type II platforms. CIF support will be used to gain a better understanding of Sery-CRISPR and to develop its applications in gene-editing.
Plant-based Carbon Fiber
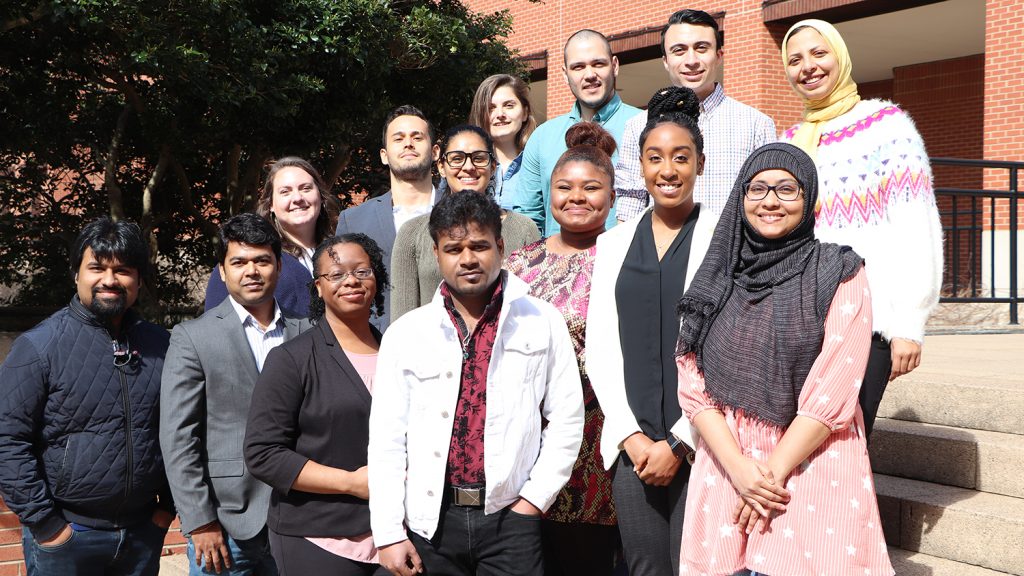
One way to make cars more fuel-efficient is to make them lighter, which manufacturers have been getting better at for decades. And one way to make cars lighter is to reinforce their frames with carbon fiber rather than steel, but due to its high cost, carbon fiber is mostly used in luxury vehicles.
Ericka Ford, of the Department of Textile Engineering, Chemistry and Science, has developed a novel process to create carbon fiber out of lignin — the polymer in plant cell walls that gives wood its rigidity — which could make it financially feasible to use carbon fiber in mainstream-vehicle frames. The technology could also lower production costs for windmills and solar panels, among other applications. CIF support will be used to develop the lignin-based carbon fiber at a semi-production scale in order to validate that it meets industry standards, like the Oak Ridge National Laboratory’s carbonization requirements.
Synthetic Gasoline from Ethane in Shale Gas
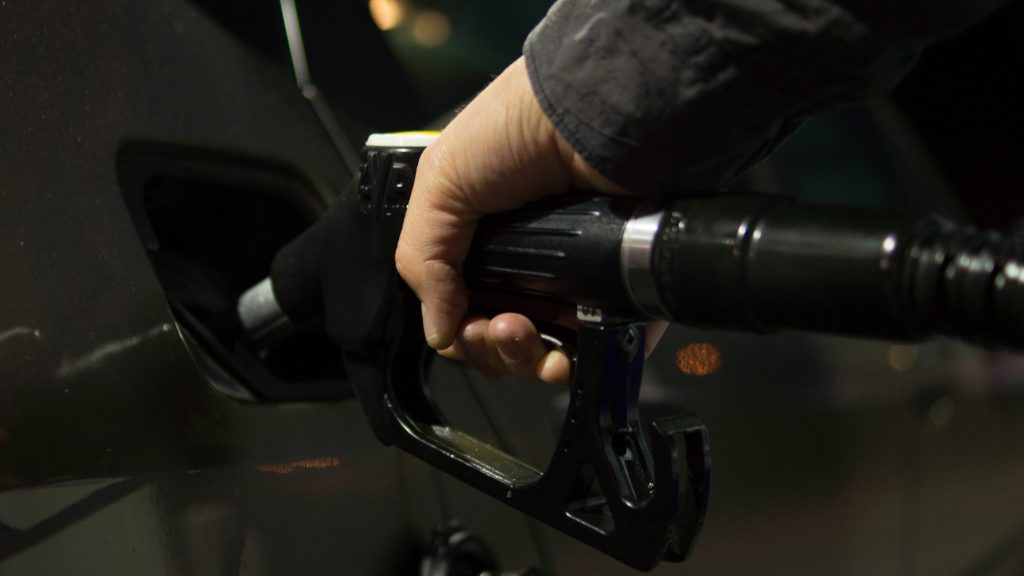
Ethane is a major byproduct of fracked shale gas, an increasingly popular form of natural gas. Up to 20% of a typical well’s output is ethane. Due to limited transportation capacity, about 210 million barrels of ethane is flared each year. Flaring not only wastes the ethane but also creates carbon pollution. Ethane can be converted to ethylene for plastics manufacturing, but the volume of ethane each well puts out is often not worth the costs to transport it from typically remote production sites to centralized conversion plants.
Fanxing Li and Luke Neal, of the Department of Chemical and Biomolecular Engineering, have developed a new technology that converts distributed ethane into synthetic gasoline, which can be easily transported out of production sites. Their technology can fit on the bed of an 18-wheeler, and the end product is close in composition to petroleum-based gasoline. CIF support will be used to validate the ethane conversion in a large-scale microchannel reactor, as required by industry.
Sustainable Toilet Paper

In the last decade, the hygiene tissue industry has struggled with higher fiber costs, a decline in the quality of recycled fibers due to digitalization, higher competition and pressures to adopt more-sustainable manufacturing methods. The cost of fibers accounts for up to 60% of total production costs.
Ronalds Gonzalez and collaborators Hasan Jameel, Lokendra Pal, Richard Venditti and doctoral student Franklin Zambrano, of the Department of Forest Biomaterials, have discovered how to make toilet paper that’s as strong and soft as today’s products while using 15% fewer fibers. Their technology, which they’ve dubbed FiRe (Fiber Reduction Technology), could lower production costs by up to 14% — potentially saving manufacturers more than $1 billion a year.
CIF support will be used to help perform commercial-scale pilot trials. Gonzalez has strong relationships with major global hygiene tissue companies, which will allow the team to take advantage of industrial-scale facilities and equipment at no cost.
Safer Gut Supplements for Livestock
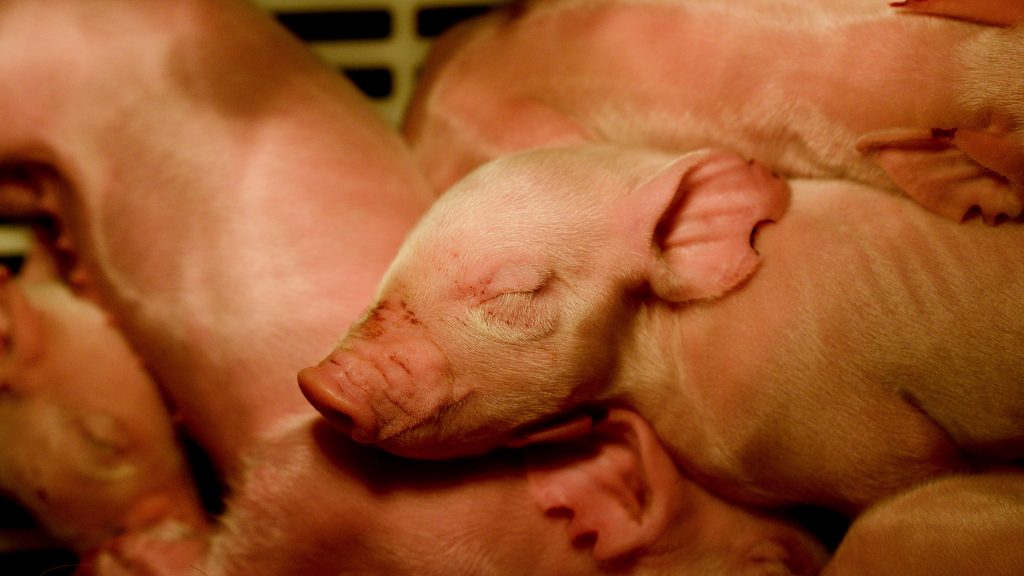
Zinc oxide (ZnO), once widely used to control gut health in livestock, has been banned in the European Union and is being restricted globally. ZnO can’t be properly digested, which is detrimental not only to animals but also to the environment when it leaves their system. With no effective replacement, EU swine farmers have seen a 25% increase in the mortality rate of their herds.
So James Martin, of the Department of Chemistry, and Jonathan Holt, of the Department of Animal Science, teamed up to create CarboZn. CarboZn encapsulates a mineral form of zinc in cellulose that can be added to feed, so the right amount of Zn can be delivered to the right portion of the animal’s digestive tract — eliminating the harmful effects to animals and the environment. The technology is being tested in pigs, but it could also potentially be used in supplements for chickens, cows, horses or even humans.
CIF support will be used to perform large-scale in vivo animal trials to test CarboZn’s efficacy and yield data that can be used for market-testing. Martin and Holt have also partnered with MBA students in the Technology Entrepreneurship and Commercialization Program, who plan to help them launch a startup and commercialize the technology.
- Categories: