Progress at the Pump
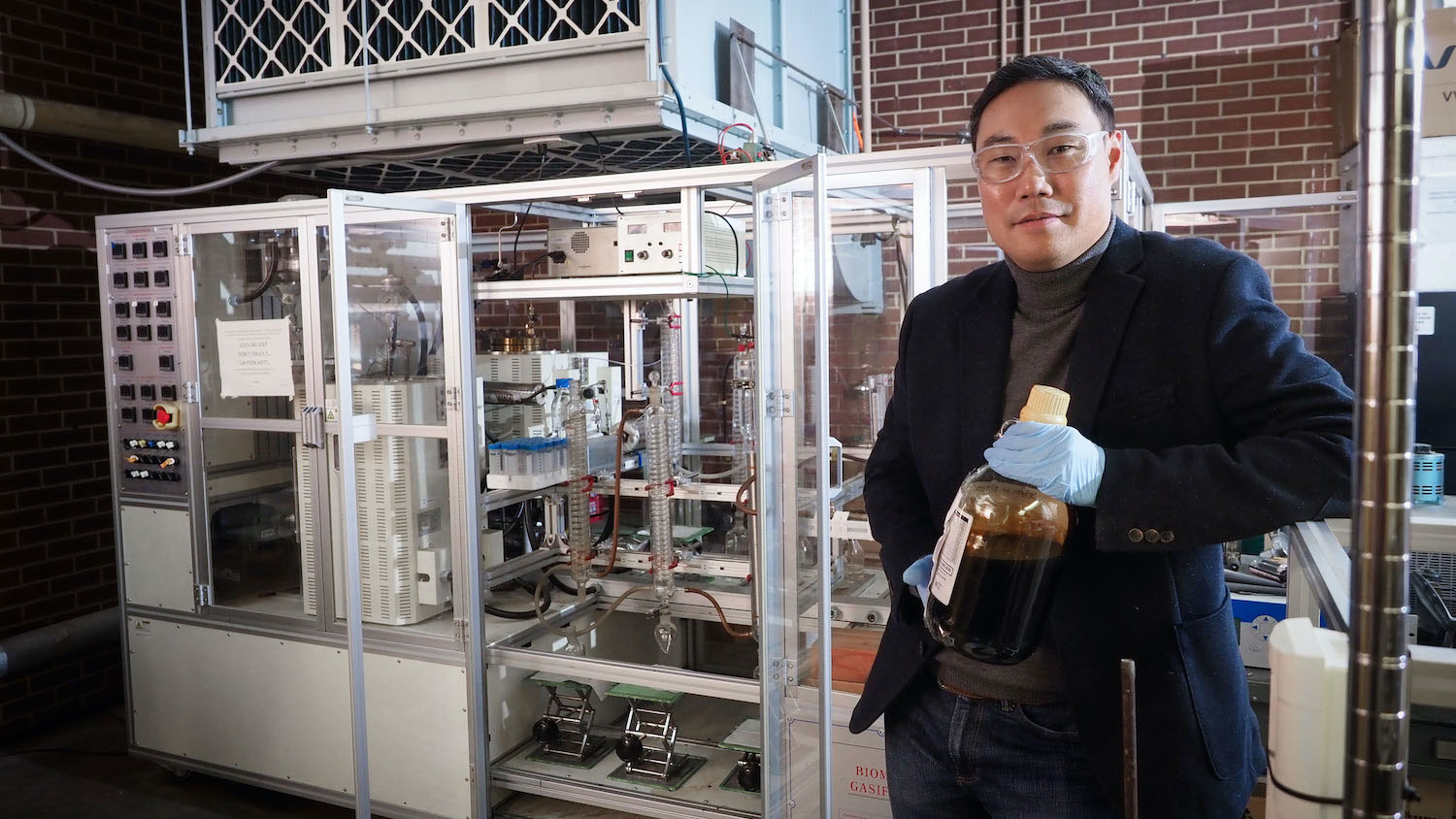
NC State feels like home to many people, but few Pack members have as strong of a connection to the university as the College of Natural Resources’ Professor Sunkyu Park. He was practically born on campus, as his parents were living in E.S. King Village at the time while his father completed his doctorate in the Department of Statistics. Then, Park’s family moved to South Korea.
Park later decided to return to the states — the United States and NC State — to pursue his own Ph.D. NC State’s paper science and engineering program was already regarded as one of the best in the world, and with his childhood connection to the university, the choice made perfect sense. He even lived in E.S. King Village again for a time, during which his own son was born.
Park completed his degree and then, in 2009, began working as an NC State faculty member.
In 2017, Park was named the E.J. “Woody” Rice Associate Professor in Paper Science and Engineering for his extraordinary service to the Department of Forest Biomaterials. This four-year professorship was established in 2008 to recognize a tenured faculty member in the department who is focused on research and teaching in biomass utilization for sustainable bioenergy and biomaterials. The Rice endowment has enabled Park to support his lab’s day-to-day operations while he pursues major advances in, among other areas, biorefinery.
“It is a very prestigious recognition in general … as far as I know, it is unusual for associate faculty to receive this kind of recognition,” said Park, who is also a University Faculty Scholar. “[The Rice professorship] provided a unique opportunity for me because, usually when we have a research contract, all of our resources are binding on that work, so it is difficult to create resources to do something else. This provides us with resources to create new initiatives, to generate some preliminary data, and that way we can prepare a grant proposal.”
One such proposal that was recently awarded: “Catalytic Upgrading of Carbohydrates in Waste Streams to Hydrocarbons.”
The Future of Fuel
Park is the lead researcher on this project, which, in conjunction with the National Renewable Energy Laboratory, seeks to turn a waste product of pulp and paper mills known as “paper sludge” into a high-performance biofuel. The three-year grant is funded by the U.S. Department of Energy’s Bioenergy Technologies Office and provides the researchers with more than $2.5 million.
Sludge fuel is created by separating carbohydrates from paper sludge and converting them into a usable form of hydrocarbon, which can then be added to jet or diesel fuel to make it more sustainable, economical and environmentally friendly. Park’s team is also seeking to reduce the production cost by integrating and optimizing the overall conversion process. This innovative technique could create approximately 150 million gallons of sludge fuel per year given the current supply of paper sludge.
That supply is quite large. Park said more than 8 million tons of paper sludge are produced in the U.S. each year, and two thirds are currently deposited into landfills. Transporting the sludge to the landfills, paying the landfill fees and covering all of the other associated expenses comes to roughly $30 per ton. The total cost of U.S. sludge disposal? Roughly $160 million. Annually.

And Park expects the cost of landfilling to rise.
“The pulp and paper industry is not a small industry; it’s actually a pretty big industry,” he said. “In terms of its production volume of printing/writing paper, packaging and tissue/towel, it is not decreasing. It is actually increasing quite a bit.”
Park said home deliveries from Amazon and other companies are a main driver of this increase. As the surge in online shopping seen during COVID-19 is likely to continue even after the pandemic ends, the amount of pulp and paper products — and, thus, paper sludge — produced will no doubt rise, too.
Thankfully, Park has the funding to find meaningful solutions to these issues. And others.
Homegrown Graphite
Lithium gets the limelight when it comes to lithium-ion batteries, but graphite plays a surprisingly large role in these rechargeable energy sources — so much so that tech giant and space pioneer Elon Musk once said the power cells in his Tesla company’s vehicles “should be called nickel-graphite, because primarily the cathode is nickel and the anode side is graphite with silicon oxide … [there’s] a little bit of lithium in there, but it’s like the salt on the salad.”
Graphite anodes can be made from natural or synthetic graphite, but both types are becoming harder to come by as more companies incorporate lithium-ion batteries into their products. At roughly $10 to $20 per kilogram, they aren’t cheap, either. To put things in perspective, Tesla reportedly spends a quarter of the production cost of a Model 3 on just the raw materials for its battery.
That growing demand led Park and another of his research teams to develop carbon materials such as bio-graphite, woody biomass (in this case, pine trees) converted into a sustainable supply of graphite. Bio-graphite has been shown to work as well as existing lithium-ion anode material and is sustainable, cost-effective and domestically sourced. If that wasn’t enough, it can also be used in nuclear reactors, supercapacitors, aerospace design and more.
The incredible potential of this research caught the attention of the U.S. Department of Energy and led to talks of a second major grant for Park, this one for four and a half years with $4 million — “Biocrude Derived Anode Materials (BDAM).” Park is currently under award negotiation with the department and expects to begin the work this summer. The project team will work to scale up the process and produce BDAM for ion batteries.
It is no stretch to say that Park’s research into environmentally and economically friendly fuel could benefit the world and everyone in it. Government funding has certainly played a part in making his work possible, but it is the E.J. “Woody” Rice Associate Professor in Paper Science and Engineering that has consistently provided him with critical resources. Above all, though, Park credits his fellow faculty members with helping him think and do the extraordinary every day.
“[I]n the Department of Forest Biomaterials, we work as a team,” Park said. “It is critical to have a diverse team with different expertise and backgrounds. Many faculty members helped me envision the process and make a connection to industries and other stakeholders. I want to say that this is a truly collaborative effort.”